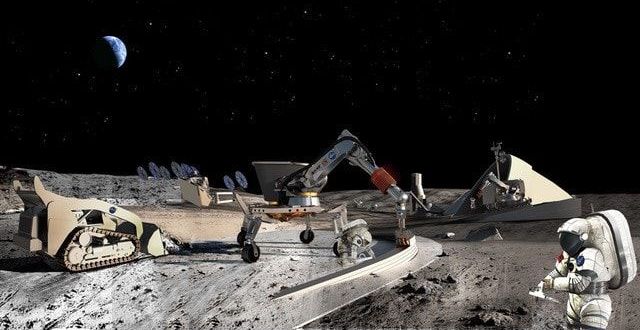
Caterpillar has been synonymous with big, heavy equipment — for farming, construction and mining — since Holt Manufacturing and C. L. Best Tractor merged in 1925 to form the Peoria, Illinois-based company. Over the years, tons of innovation have been built into the iconic yellow products, too, from the Model 20 Track-Type Tractor introduced in 1927 to the ginormous engines that helped power the Apollo 11 mission to the moon 50 years ago.
Coincidentally, one of Cat’s latest breakthroughs is self-driving, or autonomous, and remote-controlled mining equipment, which could very well find itself on the moon when NASA is scheduled to return to the lunar surface in 2024, with plans to build a permanent base near the orb’s south pole, part of the Artemis program.
Just as on terrestrial sites, Caterpillar fully or semi-autonomous bulldozers, graders, loaders and dump trucks could be utilized to build roads, housing and other infrastructure. Operator-less drilling and digging machines might mine water, oxygen-rich rocks and moon dust for use in 3D printing of various materials.