Making plastic bricks, 5 times stronger than concrete, Nzambi Matee runs Njenge Makers in Nairobi, where she turns plastic waste into bricks.
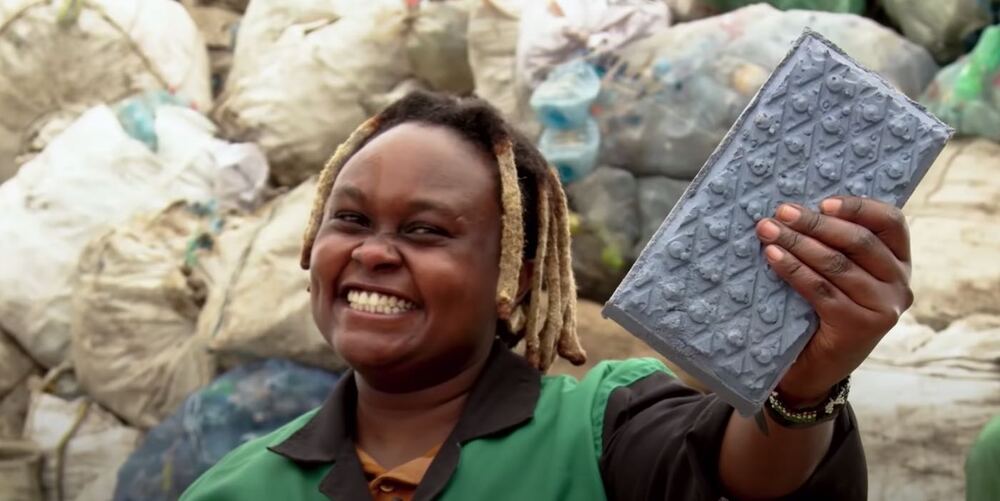
WASHINGTON — The Defense Advanced Research Projects Agency wants to hear from the space industry about their capabilities to manufacture large structures on the moon.
This is a new project that DARPA announced Feb. 5 called “Novel Orbital and Moon Manufacturing, Materials and Mass-efficient Design.”
Plastics are among the most successful materials of modern times. However, they also create a huge waste problem. Scientists from the University of Groningen (The Netherlands) and the East China University of Science and Technology (ECUST) in Shanghai produced different polymers from lipoic acid, a natural molecule. These polymers are easily depolymerized under mild conditions. Some 87 percent of the monomers can be recovered in their pure form and re-used to make new polymers of virgin quality. The process is described in an article that was published in the journal Matter on 4 February.
This can turn out to be a very important and useful invention for medical science. The elastic and adhesive glue quickly seals wounds after application, without the need of stitches or staples. The glue, called ‘Metro’, quickly seals wounds in just 60 seconds. The gel-like material of the wound glue is activated by Ultraviolet (UV) light and it dissolves shortly after. Metro glue’s elasticity makes it ideal for sealing wounds in body tissues that continually expand and relax like the heart or lungs. The glue has been successfully tested on rodents and pigs. It will soon be used in human trials. Kiran Mazumdar Shaw, who is the chairperson of Biocon — Asia’s leading Biopharmaceuticals enterprise, shared a video about the wound glue. The video by In The Know, shows how the Metro glue works.
Glue for wounds!
https://twitter.com/kiranshaw/status/1357879020440854528
New research conducted by the Okinawa Institute of Science and Technology Graduate University (OIST) has identified a specific building block that improves the anode in lithium-ion batteries. The unique properties of the structure, which was built using nanoparticle technology, are revealed and explained today in Communications Materials.
“TECLA (an acronym which stands for “Technology and Clay”) is a habitat consisting of two interconnected housing units, each covered by a semi-spherical dome. The units have been built using multiple Crane Wasp printing units operating simultaneously. Crane WASP is defined by the manufacturer as “a collaborative 3D printing system capable of printing houses” and can print various materials — such as earth-based materials, concrete mortar, and geopolymers — with a maximum speed of 300 mm/s and a maximum printing area of 50 sqm per unit. The design of the habitat features two or more “cocoon-like” housing units, whose shape vaguely resembles that of a sea urchin, in which structure, insulation, and finishes coincide. The thick raw earth walls of the units have a hollow structure consisting of several clay “waves”, which makes them at the same time relatively lightweight, resistant, and highly insulating. About 200 printing hours are required to build each unit, which consists of 350 clay layers, each 12 mm thick.”
Designed by Mario Cucinella and build by WASP, TECLA is a prototype house near Ravenna, Italy, made by 3D-printing a material based on locally-sourced clay.
3D printing is a universal process in the sense that pretty much any part that can be drawn up in a CAD program can be printed, at least within a certain resolution. Machining a part on a mill or lathe, while having the advantage of greater accuracy and material options, is a slightly less universal process in that many possible designs that exist in theory could never be machined. A hollow sphere can easily be printed, but a ball could never be milled as a single part into a hollow sphere—unless you happen to have a milling machine tiny enough to fit inside the ball. But what about biological parts, and whole animals? How universal, from a design perspective, is growth?
It was invented by David Gathu and Moses Kinyua and is powered by brain signals.
The signals are converted into an electric current by a “NeuroNode” biopotential headset receiver. This electrical current is then driven into the robot’s circuitry, which gives the arm its mobility.
The arm has several component materials including recycled wood and moves vertically and horizontally.
Juniorr Amenra.
· —3—h ·