Machines can now distinguish between 12 different types of plastic, thanks to a new camera system developed in Denmark.
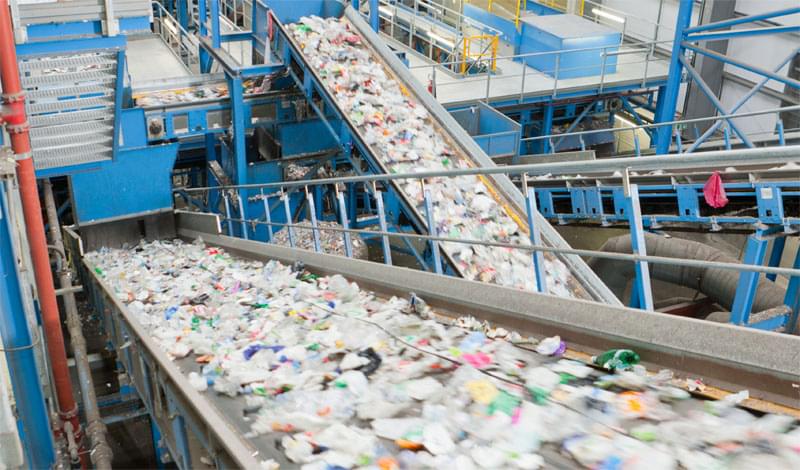
Inspired by the growth of bones in the skeleton, researchers at the universities of Linkoping in Sweden and Okayama in Japan have developed a combination of materials that can morph into various shapes before hardening. The material is initially soft but later hardens through a bone development process that uses the same materials found in the skeleton.
When we are born, we have gaps in our skulls that are covered by pieces of soft connective tissue called fontanelles. It is thanks to fontanelles that our skulls can be deformed during birth and pass successfully through the birth canal. Post-birth, the fontanelle tissue gradually changes to hard bone. Now, researchers have combined materials that together resemble this natural process. “We want to use this for applications where materials need to have different properties at different points in time. Firstly, the material is soft and flexible, and it is then locked into place when it hardens. This material could be used in, for example, complicated bone fractures. It could also be used in microrobots — these soft microrobots could be injected into the body through a thin syringe, and then they would unfold and develop their own rigid bones”, says Edwin Jager, associate professor at the Department of Physics, Chemistry and Biology (IFM) at Linkoping University.
The idea was hatched during a research visit in Japan when materials scientist Edwin Jager met Hiroshi Kamioka and Emilio Hara, who conduct research into bones. The Japanese researchers had discovered a kind of biomolecule that could stimulate bone growth under a short period of time. Would it be possible to combine this biomolecule with Jager’s materials research, to develop new materials with variable stiffness? In the study that followed, published in Advanced Materials, the researchers constructed a kind of simple “microrobot”, one which can assume different shapes and change stiffness. The researchers began with a gel material called alginate. On one side of the gel, a polymer material is grown. This material is electroactive, and it changes its volume when a low voltage is applied, causing the microrobot to bend in a specified direction.
Most toilet models flush away waste with gallons of water. Instead, the BeeVi toilet – a portmanteau of the words’ bee’ and ‘vision’ – use a vacuum pump to suck shit into an underground bioreactor, which means it uses less water. The energy-producing toilet system is much smaller than the existing flushable toilets, as it treats human excrement without using water.
The system utilizes a natural biological process to break down human waste into a dehydrated odorless compost-like material. Once these powdered feces are transferred to the Microbial Energy Production system, they can later be converted to methane, which becomes a source of energy for the building, powering a gas stove, hot-water boiler, and solid oxide fuel cell.
“If we think out of the box, faeces has precious value to make energy and manure. I have put this value into ecological circulation,” the inventor Cho Jae-weon said.
Berkeley Lab engineers have developed an all-season smart roof coating that keeps homes warm during the winter and cool during the summer without consuming natural gas or electricity. The all-season roof coating automatically switches from keeping you cool to warm, depending on outdoor air temperature.
The problem with many cool-roof systems currently on the market is that they continue to radiate heat in the winter, which drives up heating costs, explained Junqiao Wu, a faculty scientist who led the study. “Our new material – called a temperature-adaptive radiative coating (TARC) – can enable energy savings by automatically turning off the radiative cooling in the winter, overcoming the problem of overcooling,” he said.
The key to the technology is a strange compound called vanadium dioxide (VO2). In 2017, Wu and his research team discovered that electrons in vanadium dioxide behave like metal to electricity but an insulator to heat. Below about 67 degrees Celsius, vanadium dioxide is also transparent to thermal-infrared light. But once vanadium dioxide reaches 67 degrees Celsius, the material switches to a metal state, becoming absorptive of thermal-infrared light. This ability to switch from one phase to another – in this case, from an insulator to metal – is characteristic of what’s known as a phase-change material.
Efficient electrocatalysts, which are needed for the production of green hydrogen, for example, are hidden in materials composed of five or more elements. A team from Ruhr-Universität Bochum (RUB) and the University of Copenhagen has developed an efficient method for identifying promising candidates in the myriad of possible materials. To this end, the researchers combined experiments and simulation.
They published their report in the journal Advanced Energy Materials (“Unravelling Composition–Activity–Stability Trends in High Entropy Alloy Electrocatalysts by Using a Data-Guided Combinatorial Synthesis Strategy and Computational Modeling”).
A view of the sputtering machine used to produce the material library counters. (Image: Christian Nielinger)
A team of physicists from the Massachusetts Institute of Technology (MIT) has discovered a hybrid particle that could pave the way for smaller and faster electronic devices in the future.
The hybrid particle, which was found to be a mashup of an electron and a phonon (a quasiparticle formed by vibrating atoms in a material), was detected in a strange, two-dimensional magnetic substance.
Probably the most intriguing aspect of the discovery, however, is that when the scientists measured the force between the electron and phonon, they saw that the glue, or bond, was 10 times stronger than what had previously been estimated for other known electron-phonon hybrids, according to the study which has been published in the journal Nature Communications.
Circa 2020
Harnessing the destructive potential of force and rotation, cutting tools like saws, drills, and angle grinders can obliterate the superlative properties that materials work so hard to perfect. And even when materials are designed to work against the power of these tools, the materials still often fail.
So what if instead we designed materials to work with the power of cutting tools rather than against them? While that may sound counterintuitive, it is just what an international group of researchers has done—and their preliminary tests show the ceramic–metal composite material they designed resists damage beyond shallow surface cuts.
The researchers, from Durham University, University of Surrey, and University of Stirling in the U.K. and Fraunhofer Institute and Leibniz University Hannover in Germany, developed a ceramic–metal composite that, despite being just 15% as dense as steel, is nearly uncuttable. By harnessing the power of vibration, the material directs tools’ destructive energy back upon themselves, wearing the tools down before they can inflict serious damage on the material.